Slurry pumps play a crucial role in various industries, such as mining, wastewater treatment, and dredging, where the transportation of abrasive and dense slurries is a common requirement.
Engineers and operators often face a phenomenon: the pump head decreases as the flow rate increases.
We will talk about the reasons behind this and explore the implications for optimizing slurry pump performance.
Firstly, the inherent viscosity of the slurry is a primary contributor. As the flow rate escalates, the slurry’s viscosity creates an increased frictional resistance within the pump and associated piping. This friction, in turn, takes a toll on the pump head, impacting its overall efficiency.
Secondly, we can’t overlook the role of system resistance. Slurry pump systems are intricate, a maze of pipes, valves, and fittings. As flow rates climb, the resistance within this network intensifies, causing additional head loss. Disruptions to the smooth flow of the slurry, like bends, elbows, and other fittings, are the usual suspects behind this increased resistance. The pump has to put in extra work to overcome this resistance, causing a further reduction in head.
Then there’s the issue of impeller wear and erosion. Slurries are often a cocktail of abrasive particles that can wear down the pump impeller over time. When the flow rate rises, these particles impact the impeller with greater force, speeding up the wear process. A worn impeller is less efficient at generating the required head, adding to the decrease in pump performance.
Lastly, cavitation comes into play. As flow rates increase, so does the likelihood of cavitation within the pump. This process results in the formation of vapor bubbles, which collapse with considerable force, damaging the impeller and reducing the pump head. To avoid cavitation-related issues, good design and regular maintenance are paramount.
In essence, the decrease in slurry pump head with an increasing flow rate is a puzzle with multiple pieces. These include viscosity-induced friction, system resistance, impeller wear, and cavitation risks. Grasping these dynamics is vital for optimizing slurry pump performance and ensuring efficient operation across various industrial applications. Regular maintenance, sound system design, and careful material selection are the keys to addressing these challenges and extending the life of slurry pump systems.
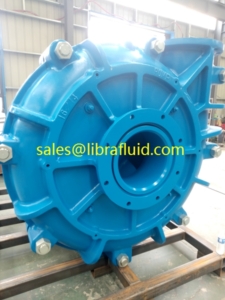